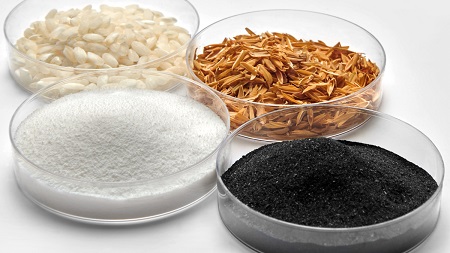
En 1994, Continental sustituyó por primera vez el negro de humo por el sílice
Lunes, 31 de marzo de 2025
Miércoles, 19 de marzo de 2025
Hace treinta años, Continental utilizó el sílice por primera vez como componente para la banda de rodadura de sus neumáticos para automóviles. La incorporación de este relleno revolucionó la seguridad de conducción y la eficiencia energética de los neumáticos, reduciendo significativamente la resistencia a la rodadura y acortando las distancias de frenado casi a la mitad.
Esto fue posible gracias a las propiedades superficiales especiales del sílice, que puede formar enlaces químicos con el polímetro de caucho. Durante la vulcanización -el proceso en el que el neumático adquiere su forma-, el sílice, junto con otros componentes, es responsable de la formación de una red muy fuerte entre las moléculas de caucho: el resultado es un neumático elástico con excelentes propiedades de seguridad. Hoy en día, el sílice ha sustituido en gran medida al negro de humo en la banda de rodadura y se ha convertido en un material indispensable en muchos compuestos de caucho para neumáticos de coches, furgonetas y vehículos de dos ruedas. Además, su producción es cada vez más sostenible gracias a un sílice que Continental utiliza, obtenida a partir de cenizas de cáscara de arroz.
"El sílice en los compuestos de caucho supuso una revolución en la tecnología de los neumáticos, ya que nos permitió reducir casi a la mitad la distancia de frenado en superficies mojadas. Hoy en día sigue siendo una enorme mejora de la seguridad", afirmó el profesor Burkhard Wies. A mediados de los años 90, trabajó en Continental en el desarrollo de los primeros neumáticos que utilizaban sílice en el compuesto de caucho y hoy dirige el departamento de Investigación Aplicada e Innovación. "Los compuestos de sílice también son buenos para el medio ambiente, ya que reducen la resistencia a la rodadura de los neumáticos, lo que significa un menor consumo de combustible para los motores de combustión y una mayor autonomía para los coches eléctricos actuales", destacó Wies.
El sílice se utiliza como material de relleno en muchas industrias. Como ejemplo, en la construcción se utiliza para la producción de hormigón y ladrillos. Este material se obtiene principalmente de la arena de cuarzo, sin embargo, el sílice cristalino no es apta para la fabricación de neumáticos. En su lugar, se utiliza un sílice 'amorfo' preparada técnicamente.
A mediados de los años 90, Continental fue uno de los primeros fabricantes de neumáticos del mundo en reconocer el potencial del sílice como relleno para esta industria y, a principios de la década, la empresa de Hannover realizó los primeros experimentos muy prometedores.
Sus propiedades se activan durante el proceso de mezclado, en el que el sílice reacciona con el aglutinante silano. En el siguiente paso, el proceso de vulcanización, la mezcla de caucho se presuriza a temperaturas de 120º a 160ºC. El neumático obtiene su aspecto característico gracias a unos moldes especiales y, al mismo tiempo, se utiliza azufre para convertir el compuesto de caucho y sílice en un caucho flexible y elástico. Esto se debe a que el azufre forma puentes entre los filamentos moleculares de cadena larga del caucho durante la vulcanización. El sílice -apoyado por el silano- forma enlaces adicionales entre los polímetros de caucho individuales, creando una red muy fuerte entre las moléculas de caucho. Esto confiere al neumático propiedades físicas como un excelente agarre sobre mojado, una buena resistencia a la abrasión y una excelente resistencia a la rodadura, a la vez que puede soportar tensiones extremas.
Las primeras pruebas en carretera en las que se utilizó el nuevo relleno entre los componentes de los neumáticos, allá por 1994, demostraron enormes mejoras en el frenado en carreteras mojadas y en la resistencia a la rodadura en comparación con el negro de humo. Un año más tarde, Continental utilizó sílice por primera vez en la producción de un neumático, el ContiEcoContact CP. En 1996, esto fue seguido por el lanzamiento del ContiWinterContact TS 770, el primer neumático de invierno con sílice en el compuesto de caucho del neumático.
"Junto con la introducción de equipos de seguridad pasiva como los cinturones de seguridad y el sistema antibloqueo de frenos, el uso de sílice en los neumáticos ha contribuido a reducir significativamente el número de víctimas en carretera”, comentó Wies.
Los desarrolladores de Continental trabajan constantemente para aumentar la seguridad, sostenibilidad y rendimiento de los neumáticos tanto en su montaje como en sus materiales utilizados. En este sentido, la empresa investiga el uso de sílice alternativo: más sostenible, con propiedades comparables y beneficios para la seguridad. La cascarilla de arroz ha demostrado ser un material de base fiable para el sílice fabricado de forma sostenible. Se trata de un subproducto de la producción de arroz que no puede utilizarse como alimento o pienso y, en comparación con materiales convencionales como la arena de cuarzo, contribuye en una producción más eficiente de sílice. El sílice procedente de las cenizas de la cáscara de arroz ya se utiliza en el neumático de producción más sostenible de Continental hasta la fecha: el UltraContact NXT.
© Canal Neumático | Aviso legal | Política de privacidad | Política de cookies
Créditos d: Alex Guimerà & d: Marc Perez